How Aluminium Fabrication Enhances Structural Integrity in Construction
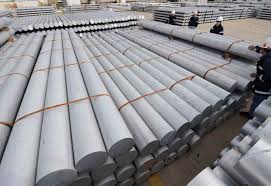
In the world of modern construction, the materials chosen for a project can significantly influence not only the aesthetic and functional outcomes but also the structural integrity of the final build. One such material that has steadily become a cornerstone of both residential and commercial architecture is aluminium. Due to its light weight, corrosion resistance, strength, and versatility, aluminium is now widely used in a variety of applications—from window frames to full structural components.
Aluminium fabrication, the process of shaping aluminium into various structural or decorative components, plays a crucial role in bringing these benefits to the construction industry. This article delves into the various ways aluminium fabrication enhances structural integrity, exploring how modern techniques and technologies contribute to stronger, safer, and more efficient buildings.
What is Aluminium Fabrication?
Aluminium fabrication involves cutting, bending, welding, assembling, and finishing aluminium fabrication into final products used in construction and other industries. Unlike steel, which is heavier and often requires additional corrosion protection, aluminium offers natural resistance to environmental wear and tear while being easy to work with. Fabrication processes are highly customizable, allowing builders to produce bespoke elements that perfectly suit their structural needs.
Common fabrication methods include:
Extrusion – shaping aluminium by forcing it through a die
Cutting and machining – using tools to shape or resize parts
Welding and joining – connecting pieces through various welding techniques
Anodizing and coating – adding surface finishes for protection or aesthetics
Why Structural Integrity Matters in Construction
Structural integrity refers to a building’s ability to withstand its intended loads without failing or deforming. Factors that affect structural integrity include:
Material properties (strength, flexibility, resistance)
Design and geometry
Environmental conditions (wind, rain, temperature)
Load-bearing capacity
Poor structural integrity can lead to serious problems: building sagging, collapse, excessive wear, and high maintenance costs. Therefore, choosing the right materials—like fabricated aluminium—can make a big difference in ensuring long-term safety and performance.
1. High Strength-to-Weight Ratio
One of aluminium’s most important advantages in construction is its high strength-to-weight ratio. Though aluminium weighs about one-third as much as steel, it can be engineered to offer comparable strength in many applications.
This characteristic allows:
Reduced structural load – Lighter buildings require less robust foundations, which can lower construction costs.
Larger spans – Aluminium beams and trusses can span wider areas without needing frequent supports, ideal for open-plan buildings.
Ease of installation – Lightweight aluminium components are easier and safer to handle on-site, reducing labor time and risk of accidents.
Modern fabrication techniques ensure that aluminium components are optimized to handle specific stress loads, bending forces, and environmental factors. Custom extrusions and reinforcements can also be added during fabrication to increase strength where needed without adding unnecessary weight.
2. Corrosion Resistance and Longevity
Another major contributor to aluminium’s role in structural integrity is its natural corrosion resistance. When exposed to air, aluminium forms a thin oxide layer that protects it from rust and environmental degradation—unlike steel, which requires frequent coating and maintenance.
Benefits of corrosion resistance in construction include:
Longer lifespan of structural components
Reduced maintenance costs over the building’s life cycle
Increased safety, especially in marine or coastal environments where salt corrosion is a concern
Aluminium can also be further protected through anodizing or powder coating, both common in the fabrication process. These finishing methods enhance the material’s resistance to wear, UV rays, and chemical exposure—further improving structural integrity over time.
3. Versatility in Design and Custom Fabrication
Unlike concrete or steel, aluminium is highly malleable. It can be extruded into custom shapes, machined into precise forms, and welded or riveted to form complex assemblies. This allows architects and engineers to design components that exactly meet performance and load requirements.
Examples of customized aluminium fabrication improving structural performance:
Specialized beams or brackets for complex roofing systems
Reinforced curtain wall frames for high-rise buildings
Custom support systems for bridges or overhangs
Because aluminium can be precisely fabricated to tight tolerances, the resulting components fit together with high accuracy. This tight fit reduces stress concentrations, movement, and wear at joints—all of which enhance the building’s structural integrity.
4. Thermal Expansion and Structural Stability
All materials expand and contract with temperature changes, but the rate at which they do so varies. Aluminium has a relatively higher coefficient of thermal expansion, meaning it expands more than steel or concrete when heated. While this might seem like a disadvantage, modern aluminium fabrication techniques account for this property during the design phase.
Properly designed aluminium structures can accommodate thermal movement without causing cracks or warping, especially when:
Expansion joints are integrated into framing systems
Sliding connectors or flexible joints are used in load-bearing areas
Accurate simulations are used in the engineering process
This adaptability ensures the material can withstand seasonal changes or fluctuating indoor/outdoor temperatures without losing its structural integrity.
5. Fire Safety and Non-Combustibility
While aluminium melts at lower temperatures compared to steel (around 660°C vs. 1370°C), it does not burn or emit toxic gases. This property is particularly valuable in the construction of high-rise buildings, transportation hubs, and public facilities.
Modern aluminium components can be fabricated with:
Fire-resistant coatings
Thermal barriers
Non-combustible insulation layers
These enhancements make aluminium suitable for use in fire-rated structural assemblies, improving the overall safety and resilience of a building in the event of a fire.
6. Prefabrication and On-Site Efficiency
The shift toward off-site construction and modular building systems has increased the demand for materials that can be prefabricated efficiently. Aluminium is ideal for this model due to its:
Ease of transport (lightweight nature)
Precision manufacturing
Ease of assembly/disassembly
Prefabricated aluminium components can be built in controlled factory settings using advanced fabrication equipment, ensuring consistent quality and tight tolerances. These components can then be quickly assembled on-site, reducing construction timelines and the likelihood of errors or misalignments that might compromise structural integrity.
7. Seismic and Wind Load Performance
Aluminium’s flexibility and strength make it suitable for regions prone to earthquakes or high winds. In seismic zones, materials must be able to absorb shock and dissipate energy without fracturing. Aluminium, when fabricated into properly engineered systems, can do just that.
Examples of structural enhancements for seismic zones:
Flexible curtain wall systems
Shock-absorbing aluminium joints
Flexible frame connectors
Similarly, for wind-resistant buildings (especially skyscrapers), aluminium’s light weight reduces the overall mass of the building, minimizing sway while providing strong, rigid frames for cladding, windows, and balconies.
8. Integration with Other Materials
Fabricated aluminium is often used in combination with other materials such as glass, steel, or composites. This integration enhances both performance and design. When used correctly, aluminium can improve the structural interface between materials with different properties.
Examples:
In glass facades, aluminium mullions offer strong yet slim support.
In composite panels, aluminium skins provide durability while the core offers insulation.
In hybrid load-bearing systems, aluminium can act as a lightweight framing element supporting heavier steel or concrete cores.
Proper fabrication ensures these material interfaces are structurally sound and resistant to stress, temperature changes, and environmental exposure.
9. Sustainability and Lifecycle Performance
A structurally sound building is one that not only stands firm but also maintains its integrity for decades with minimal environmental impact. Aluminium contributes to this by being:
100% recyclable without loss of properties
Low maintenance, needing fewer repairs or replacements
Compatible with sustainable building certifications like LEED and BREEAM
Because of its long life cycle and low maintenance needs, fabricated aluminium parts help improve a building’s overall resource efficiency, which is a key part of structural sustainability.
Real-World Applications of Aluminium Fabrication in Structural Integrity
Let’s look at some real-life examples where aluminium fabrication has played a pivotal role:
● High-Rise Buildings
Aluminium-framed curtain walls and window systems offer high strength with reduced weight, improving the load distribution and stability of tall structures.
● Bridges
Aluminium is used in pedestrian and vehicle bridges where light weight and corrosion resistance are essential, reducing load on supports and minimizing maintenance.
● Airports and Stadiums
These large-span structures rely on fabricated aluminium trusses and roof systems that are strong, lightweight, and weather-resistant.
● Modular Homes
Aluminium framing systems are increasingly used in prefab and modular homes for their easy handling and fast assembly.
Conclusion
Aluminium fabrication is more than just a manufacturing process—it’s a gateway to achieving greater structural integrity in modern construction. From its impressive strength-to-weight ratio and corrosion resistance to its adaptability, sustainability, and performance in harsh environments, aluminium is reshaping how we build the future.
With advanced fabrication methods, engineers and architects can customize aluminium elements to meet even the most demanding structural requirements. Whether it’s supporting the roof of a stadium, the walls of a skyscraper, or the frame of a prefabricated home, aluminium proves to be a reliable and forward-thinking choice in construction.
As innovation continues and building codes evolve, aluminium will remain at the forefront—ensuring that the buildings we design today are safer, stronger, and more resilient for tomorrow.